مخزن تحت فشار با تحمل فشار 20 بار
- درباره ما
- پست تک

مخزن تحت فشار با تحمل فشار 20 بار
مخازن تحت فشار به عنوان یکی از اجزای کلیدی در بسیاری از صنایع، نقش
حیاتی در ذخیرهسازی و انتقال مایعات و گازهای فشرده دارند. این مخازن به
طور خاص برای تحمل فشارهای بالا طراحی و ساخته میشوند. در این مقاله
به بررسی مخازن تحت فشار با تحمل فشار 20 بار خواهیم پرداخت، از جمله
کاربردها، مواد مورد استفاده، فرایند ساخت و نکات ایمنی.
کاربردهای مخازن تحت فشار
مخازن تحت فشار با تحمل 20 بار به طور گستردهای در صنایع مختلف استفاده
میشوند. برخی از کاربردهای اصلی این مخازن عبارتند از: صنایع نفت و گاز: این
مخازن برای ذخیره و انتقال گازهای طبیعی، پروپان، بوتان و دیگر گازهای فشرده
استفاده میشوند. صنایع شیمیایی: در این صنایع، مخازن تحت فشار برای ذخیره
و حمل مواد شیمیایی خطرناک و واکنشزا به کار میروند. صنایع غذایی و نوشیدنی:
در این صنایع، از مخازن تحت فشار برای تولید و ذخیره گازهای مصرفی مانند دی
اکسید کربن در فرآیندهای تولید نوشیدنیهای گازدار استفاده میشود. صنایع
داروسازی: این مخازن برای ذخیرهسازی و انتقال گازهای پزشکی مانند اکسیژن
و نیتروژن استفاده میشوند. تأسیسات تصفیه آب:مخازن تحت فشار برای ذخیره
سازی آب تحت فشار و استفاده در سیستمهای آبیاری و تصفیه آب کاربرد دارند.
مواد مورد استفاده در ساخت مخازن تحت فشار
انتخاب مواد مناسب برای ساخت مخازن تحت فشار بسیار حیاتی است، زیرا باید
بتوانند فشارهای بالا را تحمل کنند و در برابر خوردگی و زنگزدگی مقاوم باشند.
برخی از مواد رایج در ساخت این مخازن عبارتند از: فولاد کربنی: این ماده به دلیل
مقاومت بالا و هزینه نسبتاً پایین، به طور گستردهای در ساخت مخازن تحت فشار
استفاده میشود. فولاد کربنی برای ذخیرهسازی گازها و مایعات تحت فشار مناسب
است. فولاد ضد زنگ: این ماده به دلیل مقاومت بسیار خوب در برابر خوردگی و زنگ
زدگی، به خصوص در محیطهای خورنده و برای ذخیرهسازی مواد شیمیایی مورد
استفاده قرار میگیرد. آلیاژهای نیکل: این آلیاژها برای کاربردهای خاصی که نیاز به
مقاومت بالا در برابر حرارت و خوردگی دارند، استفاده میشوند. مواد کامپوزیتی: این
مواد، ترکیبی از الیاف و رزینهای مقاوم هستند که به دلیل وزن سبک و مقاومت بالا،
در برخی کاربردهای خاص استفاده میشوند.
فرآیند ساخت مخازن تحت فشار
ساخت مخازن تحت فشار با تحمل 20 بار نیاز به دقت و کنترل کیفیت بالا دارد. فرآیند
ساخت شامل مراحل زیر است: طراحی و مهندسی: محاسبات فنی: در این مرحله،
مشخصات فنی مخزن شامل ابعاد، ضخامت دیوارهها و نوع مواد مورد استفاده تعیین
میشود. محاسبات فنی باید مطابق با استانداردهای معتبر بینالمللی انجام شود.
نقشهکشی: نقشههای فنی و مهندسی تهیه میشوند که شامل جزئیات ساختاری
و نحوه مونتاژ قطعات است. انتخاب مواد و برش: انتخاب مواد اولیه:بر اساس محاسبات
فنی، مواد مناسب انتخاب میشوند. برش مواد: مواد اولیه به ابعاد و شکلهای مورد
نیاز برش داده میشوند. این برشها باید دقیق و بدون نقص باشند. شکلدهی و
جوشکاری:شکلدهی قطعات: قطعات برش دادهشده با استفاده از دستگاههای شکل
دهی به شکلهای مورد نیاز تبدیل میشوند. جوشکاری:قطعات شکلگرفته با استفاده
از روشهای جوشکاری مناسب به هم متصل میشوند. نوع جوشکاری به نوع ماده و
شرایط عملیاتی مخزن بستگی دارد. بازرسی و آزمایش:بازرسی چشمی: تمامی جوش
ها و اتصالات به صورت چشمی بازرسی میشوند تا از کیفیت آنها اطمینان حاصل شود.
آزمایش فشار مخزن تحت فشار بالا آزمایش میشود تا از تحمل فشار 20 بار اطمینان
حاصل شود. این آزمایشها شامل فشارهای هیدرواستاتیک و پنوماتیک است. آزمایش
نشتی: مخزن برای اطمینان از عدم نشتی در اتصالات و جوشها آزمایش میشود. عایق
بندی و پوششدهی: عایقبندی:در صورت نیاز، مخزن با مواد عایق پوشش داده میشود
تا از دماهای بالا یا پایین محافظت شود. پوششدهی: مخزن با پوششهای مقاوم در برابر
خوردگی و زنگزدگی پوشش داده میشود. نصب و راهاندازی: انتقال به محل نصب:پس از
تکمیل مراحل ساخت، مخزن به محل نصب منتقل میشود. نصب:مخزن به سیستمهای
مورد نیاز متصل میشود و راهاندازی انجام میشود.
نکات ایمنی در ساخت و استفاده از مخازن تحت فشار
رعایت استانداردهای طراحی:طراحی مخازن باید مطابق با استانداردهای معتبر بینالمللی
انجام شود تا از ایمنی و عملکرد بهینه آنها اطمینان حاصل شود.
آزمایشهای دورهای:انجام آزمایشهای دورهای برای بررسی سلامت مخازن و اطمینان از
عملکرد صحیح آنها ضروری است. آموزش کارکنان: کارکنانی که با مخازن تحت فشار کار میکنند
باید آموزشهای لازم در زمینه ایمنی و استفاده صحیح از مخازن را دریافت کنند. کنترل کیفیت:
تمامی مراحل ساخت باید تحت نظارت دقیق کنترل کیفیت انجام شود تا از تولید مخازن با کیفیت
و ایمن اطمینان حاصل شود.
نتیجهگیری
مخازن تحت فشار با تحمل فشار 20 بار نقش حیاتی در بسیاری از صنایع ایفا میکنند. این
مخازن برای ذخیرهسازی و انتقال مایعات و گازهای فشرده طراحی شدهاند و باید بتوانند
فشارهای بالا را تحمل کنند. انتخاب مواد مناسب، رعایت استانداردهای ایمنی و انجام آزمایش
های دقیق از جمله عواملی هستند که در ساخت مخازن با کیفیت و ایمن نقش اساسی دارند.
با رعایت این نکات، میتوان از عملکرد بهینه و ایمن مخازن تحت فشار در صنایع مختلف اطمینان
حاصل کرد.
ضخامت مخازن ساخته شده 8 میلیمتر است … برای سفارش انواع مخازن آب، هوایی،
تحت فشار و … به بخش تماس با ما مراجعه کنید.
مقالات اخیر
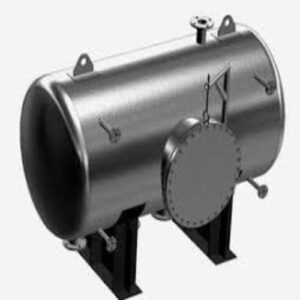
ساخت انواع منبع

مخزن تحت فشار با تحمل فشار 20 بار

ساخت انواع مخازن هوایی،پرس،نورد،لبه خم
